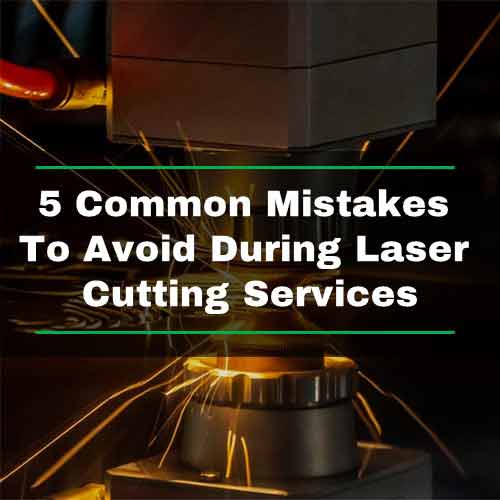
With this technological advancement, the metal cutting process is not a tough job anymore. As it is now going through laser beam emission. A laser cutting process needs accuracy over numerous factors like material category, depth, measurement, and others. However, the correct settings might affect the laser cutting precision. So, we shall be discussing the top 5 common mistakes that should be avoided during industrial cutting services:
What are some common issues with laser cutting?
- Material thickness: A perfect laser cutting service also depends on the material thickness.
- Lack of ventilated area: A CNC laser machine needs proper ventilation, as the laser beam emission emits harmful gases or fumes. That might be toxic and greatly contribute to chronic poor health effects on the individuals working there.
- Lack of accurate setting: for proceeding with accurate and precise cutting proficiency, an accurate setting, designing works, and other factors are responsible.
- Cutting depth uncertainty: The cutting depth consideration before the laser cutting process takes an important part.
What are the top 5 common mistakes that should be avoided?
A CNC laser machine is fully automatic and laced with laser beam technology. So, to get fast and accurate laser cutting performance, we need to follow a few instructions and avoid any mistakes.
1. Not wearing protective gear: Laser cutting service work is a responsible job that needs extra precautions to get damage-free work. To process the prerfect laser cutting work, we must ensure about all the protections. Here are a few of the safety considerations to follow to get better results in the future:
- Use of protective eyewear to avoid sparks or unnecessary hot splatter.
- Use of protective gas filters to protect from harmful gaseous emission and wearing of face masks.
- Use of fire extinguishers to reduce any further possibilities of future accidents caused due to the exposure of air and fires.
2. Not selecting appropriate material: Once you select an appropriate material for the laser cutting, designing, and blending work. it is getting more easier for the CNC programming to adjust the current tool setting over its requirements.
3. Failure to analyze the cutting-edge work progress: To get a work perfection we need to analyze the laser cutting work progress. It includes correct machine setting, placing materials under the laser beam emissions, and similar others.
4. Lack of proper design: A well-designed design facilitates proportionate operation on all dimensions and orientations. As a result, there won’t be any possibility of damaged or uneven edges. All the creation of complex designs with the computer controls in CNC machines is easy.
5. Lack of skilled operators: A skilled worker helps to develop the best design and applies the proper machine setting for the specified material. Additionally, having strong operational abilities is important for modifying the required settings and the production unit.
Frequently Asked Questions
Q1. How do I manage the laser cutting machine’s measuring irregularities?
Answer: Although to get cutting precision, CNC software is capable enough. However, we need to check for all the required adjustments. Below are the some important points:
- tightening of X and Y screw seats .
- All the hardware parts should be perfect, like the beam, lens, nozzle, etc.
Q2. How does using incorrect machine settings affect working perfection?
Yes, a bad setting over the CNC laser machines can drastically impact the cutting material, leaving deformities all over. In addition, it also affects the safety concerns during the laser cutting services.
Q3. What are the safety measures required for operating a laser-cutting machine?
An operator should wear all the protective gear like the Goggle, gloves, and apron to carry forward with the laser cutting services operations. Also, all kinds of protocols that come under Personal Protective Equipment (PPE) guidelines need to be followed strictly.